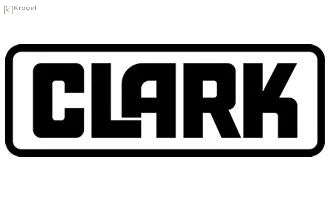
Clark Shop Manual FD-17000, FD-19000, FD-24000 Series Drive Axle
Share
Clark Shop Manual: FD-17000, FD-19000, FD-24000 Series Drive Axle
Clark Equipment Company (CLARK) has warranted to the Distributor (Seller) who, pursuant to agreement with CLARK, hereby, on its own behalf, warrants to the Buyer each new CLARK product to be free from defects in material and workmanship under normal use and maintenance as herein provided.
Distributor‘s sole obligation under this warranty shall be limited to repairing, replacing or allowing credit for, of Distributor‘s option, any port which under normal and proper use and maintenance proves defective in material or workmanship within six (6) months after delivery to or one thousand (1,000) hours of use by Buyer, whichever shall occur first; provided, however, thot (i) the product is placed in use not later than one year after shipment from CLARK‘S plant; (ii) that notice of any such defect and satisfactory proof thereof is promptly given by Buyer to Distributor; and (iii) such material shall have been returned to Distributor, with transportation charges prepaid and found by Distributor to hove been defective.
This warranty does not apply in respect of damage to or defects in any product caused by overloading or other misuse, neglect or accident, nor does this warranty apply to any product which has been repaired or altered in any way which, in the sole judgment of Distributor, affects the performance, stability or general purpose for which it was manufactured.
THIS WARRANTY IS IN LIEU OF ALL OTHER WARRANTIES (EXCEPT OF TITLE), EXPRESSED OR IMPLIED, AND THERE ARE NO WARRANTIES OF MERCHANTABILITY OR OF FITNESS FOR A PARTICULAR PURPOSE. IN NO EVENT SHALL DISTRIBUTOR BE LIABLE FOR CONSEQUENTIAL OR SPECIAL DAMAGES.
This warranty does not apply to parts or trade accessories not manufactured by CLARK, or attachments not manufactured or sold by CLARK. Buyer shall rely solely on the existing warranties, if any, of the respective manufacturers thereof.
IMPROVEMENTS
It is CLARK’S policy to constantly strive to improve its products. The right therefore is reserved to make changes in design and improvements whenever it is believed the efficiency of the product will be improved thereby, but with- out incurring any obligation to incorporate such improvements in any product which has been shipped or is in service
The axle assembly is a full floating spiral bevel type with further reduction provided by planetary gear set within the wheel hub.
PRIMARY REDUCTION
The spiral bevel pinion and ring gear transmit power through the center differential pinions and side gears to the axle shaft. The spiral bevel differential assembly is mounted on tapered roller bearings which are adjusted by positioning of the two threaded adjusting nuts mounted in the differential carrier cap assembly. The tapered roller pinion bearing preload is adjusted and maintained by a hardened and prevision ground spacer positioned between inner and outer bearings. Spacer is selected at assembly.
SECONDARY REDUCTION
In the wheel hub, a self-centering sun gear is spline fitted to the axle shaft and drives three planetary pinion gears. These gears in turn mesh with and react against a rigidly mounted internal ring gear. The planet gears rotate on needle roller bearings mounted on hardened and ground pins located in the planet carrier which in turn drives the wheel hub. Positive lubrication keeps all moving parts bathed in lubricant to reduce friction, heat, and wear.
Broke assemblies are hydraulically operated and are mounted within the brake drum. Hydraulic pressure is provided to the wheel cylinder by a brake master cylinder actuated when pressure is applied to the brake pedal mounted in the floorboard of the operator’s compartment.
Axle Application
Following is a list of axles covered in this manual and the application of these axles.
Part Number |
Model Number |
Model Usage |
130064 |
FD- 17000 |
75A-I, 85A- I |
130068 |
FD-24000 |
125A-I |
130069 |
FD-24000-1 |
125A-I |
131076 |
FD- 17600 |
7SA-II, (75A-I) |
131078 |
FD-19000 |
85A-II, (85A-I) |
131079 |
FD-24500 |
125A- II, (125A-I) |
131597 |
FD- 17600-4 |
75A-III |
131599 |
FD-19000-2 |
85A-III |
DIFFERENCES IN MODELS
The following differences exist among the axles covered in this manual:
Part No. |
Differential Ratio |
Differential Pinion Spiral |
Total Axle Ratio |
Brake Size |
Parking Brake Type |
130064 | 6.333:1 | L.H. | 22.349:1 | 16-1/4 x 2-1/2 | Wheel |
130068 | 6.166:1 | L.H. | 22.611:1 | 16-1/4 x 2-1/2 | Wheel |
120069 | 6.166:1 | L.H. | 22.611:1 | 16-1/4 x 2-1/2 | Wheel |
131076 | 6.333:1 | L.H. | 22.353:1 | 17-1/4 x 4 | Differential |
131078 | 6.333:1 | L.H. | 22.353:1 | 17-1/4 x 4 | Differential |
1310079 | 6.166:1 | L.H. | 22.611:1 | 17-1/4 x 4 | Differential |
131597 | 4.857:1 | L.H. | 17.143:1 | 17-1/4 x 4 | Differential |
131599 | 4.857:1 | L.H. | 17.143:1 | 17-1/4 x 4 | Differential |
LUBRICATION
Proper lubrication is necessary to assure long periods of trouble-free operation. Not only is it important that the required lubrication schedule be maintained, but also that the proper type of lubricant be sued. The following are the only lubricants recommended for use in these axles. Consult applicable Operator’s Manual for machine model involved for capacities and lubrication schedules.
DIFFERENTIAL AND PLANETARIES
*SAE 90 Extreme Pressure Gear Lube, SCL Type (Sulfo-Chloro-Lead), per MS•8 Specifications given herein.
*Note: When operating at ambient temperatures consistently below 0° F, use SAE 80 and when consistently above 100° F, use SAE 140. SAE 80 and SAE 140 grades when used should contain like additives specified for SAE 90 grade.
EXTREME PRESSURE GEAR LUBE
Specifications MS-8
Lubricants purchased under this specification shall be a well-refined mineral oil properly compounded with sulphur-chlorine-lead type extreme pressure additives. They shall be free of filters or abrasives, such as fuller’s earth, talc, graphite, cork, etc. They shall be stable, non-abrasive, and non-corrosive whether or not in the presence of small percentages of water.
Physical and chemical properties
S.S.U. @ 210° F | 90-100 Seconds |
S.S.U. @ 100° F | 1400 Seconds Max. |
A.P.I. Gravity | 14.4-15.9 Degrees |
Pour Point | -10° F. Max. |
Flash Point | 350° F. Min. |
Fire Point | 400° F. Min. |
Sulphur (Added) | 1.20% Min. |
Sulphur (Total) | 3.00% Min. |
Chlorine | 1.20% Min. |
Lead as Lead Oxide (Pb0) | 2.00% Min. |
Moisture | 0.20% Max. |
Load Carrying Capacity | |
Timken Test Lever Load | 70 lbs. Min. |
Timken Abrasion Test (Total Loss) | 2.0 mg. Max |
Heating Test | |
Evaporation Loss | 4.0% Max |
Viscosity Increase | 10.0% Max. |
Exploded Views
To supplement the illustrations provided in the overhaul section of the manual, exploded view illustations are supplied. Legends, keyed to the index numbers on the illustrations, are adjacent to the illustrations to aid in parts identification on the axles. The exploded views are as follows:
Fig. A Axle Assembly, Exploded View
Fig. B Differential and Carrier Assembly, Exploded
Fig. C Brake Assembly, Exploded View
Fig. D Planet Spider Assembly, Exploded View
The following compounds, or their equivalent, are required for the overhaul of FD-17000, FD-19000, and FD-24000 series axles:
Material |
Use |
Lubriplate | Apply to lips of all oil seals at reassembly |
Mixture of Red Lead and Linseed Oil | Paint ring gear teeth to check for proper differential gear and pinion engagement |
Never-Seez Compound | Apply to eccentric anchor pins of brake |
Permatex No. 2 |
Used for numerous sealing applications. |
Fig A Axle Assembly
Item Number |
Description |
Number Required |
1 | Housing, Axle | 1 |
2 | Breather, Axle Housing | 1 |
3 | Plug, Housing Expansion | 1 |
4 | Plug, Housing Filler | 1 |
5 | Nut, Wheel Stud | 20 |
6 | Shaft, Axle | 2 |
7 | Hub Assembly | 2 |
8 | Plug, Planet Filler | 2 |
9 | Cup, Outer Hub Bearing | 2 |
10 | Cone, Outer Hub Bearing | 2 |
11 | Hub, Internal Gear | 2 |
12 | Gear, Internal | 2 |
13 | Nut, Inner Spindle | 2 |
14 | Lock, Spindle Nut | 2 |
15 | Nut, Outer Spindle | 2 |
16 | Bolt, Internal Gear to Hub | 16 |
17 | Planet Spider Assembly | 2 |
18 | Lockwasher, Puller Hole Bolt | 4 |
19 | Bolt, Planet Puller Hole | 4 |
20 | Gear, Sun | 2 |
21 | Ring, Sun Gear Retaining | 2 |
22 | Washer, Sun Gear Thrust | 2 |
23 | Cup Assembly, Sun Gear Thrust | 2 |
24 | Plug, Thrust Cap | 2 |
25 | Bolt, Thrust Cap | 12 |
26 | Lockwasher, Thrust Cap | 12 |
27 | Bolt, Planet Spider to Hub | 20 |
28 | Washer, Planet Spider to Hub | 20 |
29 | Cup, Inner Hub Bearing | 2 |
30 | Cone, Inner Hub Bearing | 2 |
31 | Seal, Hub Oil | 2 |
32 | Catcher, Oil | 2 |
33 | Spindle | 2 |
34 | Drum, Brake | 2 |
35 | Brake Assembly | 2 |
36 | Bolt, Spindle and Brake Attaching | 18 |
37 | Washer, Drum to Hub Bolt | 24 |
38 | Bolt, Brake Drum to Hub | 24 |
39 | Washer, Spindle and Brake Attaching | 18 |
40 | Nut, Spindle and Brake Attaching | 18 |
41 | Nut, Wheel | 20 |
42 | Stud, Wheel | 20 |
43 | Plug, Housing Drain | 1 |
44 | Washer, Carrier to Housing | 8 |
45 | Dowel, Carrier Stud | 3 |
46 | Washer, Carrier Stud | 3 |
47 | Nut, Carrier Stud | 3 |
48 | Bolt, Carrier to Housing | 8 |
49 | Differential and Carrier Assembly | 1 |
50 | Bolt, Carrier to Housing | 3 |
51 | Washer, Carrier to Housing | 3 |
52 | Stud, Carrier to Housing | 3 |
Fig B - Differential and Carrier Assembly
Differential and Carrier Assembly
Item Number |
Description |
Number Required |
1 | Nut, Differential Adjusting | 2 |
2 | Lock, Differential Adjusting Nut | 2 |
3 | Lockwasher, Differential Adjusting Nut Lock | 2 |
4 | Bolt, Differential Adjusting Nut Lock | 2 |
5 | Cone, Differential Bearing | 2 |
6 | Nut, Ring Gear Bolt | 12 |
7 | Differential Case, Flange Half | 1 |
8 | Ring Gear | 1 |
9 | Bolt, Ring Gear | 12 |
10 | Washer, Side Gear Thrust | 2 |
11 | Washer, Differential Pinion Thrust | 4 |
12 | Pinion, Differential | 4 |
13 | Spider, Differential | 1 |
14 | Gear, Differential Side | 1 |
15 | Differential Case, Plain Half | 1 |
16 | Bolt and Nut, Differential Case | 8 |
17 | OMIT – Not Applicable This Model | 0 |
18 | Bearing, Inner Pinion | 1 |
19 | Pinion | 1 |
20 | Bolt and Washer, Differential Carrier Cap | 4 |
21 | Cap, Differential Carrier – See 22 | 1 |
22 | Carrier Assembly, Differential | 1 |
23 | Cone, Center Pinion Bearing | 1 |
24 | Cup, Center Pinion Bearing | 1 |
25 | Spacer, Pinion Bearing | 1 |
26 | Shim, Pinion Bearing Case – 0.004”, 0.007”, 0.010” | As Required |
27 | OMIT – Not Applicable This Model | 0 |
28 | Cage Assembly, Pinion Bearing | 1 |
29 | Cup, Outer Pinion Bearing | 1 |
30 | Cone, Outer Pinion Bearing | 1 |
31 | Retainer, Pinion Oil Seal | 1 |
32 | Bolt, Brake Drum to Flange | 8 |
33 | Parking Brake Assembly | 1 |
34 | Lockwasher Brake Drum to Flange | 8 |
35 | Nut, Brake Drum to Flagne | 8 |
36 | Nut, Pinion Shaft | 1 |
37 | Cotter, Pinion Shaft Nut | 1 |
38 | Washer, Pinon Shaft | 1 |
39 | Flange, Companion | 1 |
40 | Bolt and Lockwasher, Brake Attaching | 4 |
41 | Bolt and Lockwasher, Oil Seal Retainer | 8 |
42 | Seal, Pinion Oil | 1 |
43 | Gasket, Pinion Oil Seal | 1 |
44 | Screw, Differential Thrust | 1 |
45 | Lock, Thrust Screw | 1 |
46 | Nut, Differential Thrust Screw | 1 |
47 | Cup, Differential Bearing | 1 |
Fig C - Brake Assembly
Brake Assembly
Item Number |
Description |
Number Required |
1 | Lining, Brake Shoe | 2 |
2 | Shoe, Brake | 2 |
3 | Spring, Brake Shoe Return | 1 |
4 | Wheel Cylinder | 1 |
5 | Lockwasher, Wheel Cylinder Mounting | 2 |
6 | Bolt, Wheel Cylinder Mounting | 2 |
7 | Spider Assembly, Brake | 1 |
8 | Pin Assembly, Brake Shoe Adjusting | 2 |
9 | Washer, Brake Shoe Adjusting Pin | 2 |
10 | Nut, Anchor Pin | 2 |
11 | Lockwasher, Anchor Pin Nut | 2 |
12 | Washer, Cam Spring | 2 |
13 | Spring, Brake Shoe Adjusting | 2 |
14 | Cam, Shoe Adjusting | 2 |
15 | Shoe Assembly, Brake | 2 |
16 | Bushing, Brake Shoe | 2 |
17 | Pin, Brake Shoe Anchor | 2 |
18 | Ring, Anchor Pin Retaining | 2 |
19 | Strut, Anchor Pin | 1 |
20 | Rivet, Lining to Shoe | 28 |
Fig D - Planetary Assembly
Planet Spider Assembly
Item Number |
Description |
Number Required |
1 | Washer, Pinion Thrust | 3 |
2 | Roller, Pinion Needle | 75 |
3 | Spacer, Pinion Roller | 3 |
4 | Pinion, Planet | 3 |
5 | Roller, Pinion Needle | 75 |
6 | Washer, Pinion Thrust | 3 |
7 | Shaft, Pinion | 1 |
8 | Ball, Pinion | 3 |
9 | Spider, Planet | 1 |
The Clark Shop Manual for the FD-17000, FD-19000, and FD-24000 Series Drive Axle is an essential guide for anyone working on these specific models. If you are involved in the maintenance or repair of these heavy-duty drive systems, this manual will provide you with a detailed roadmap. Because every procedure must be followed precisely to ensure the reliability of the drive axle, this manual is invaluable.
In this comprehensive guide, the Clark Shop Manual delves into various aspects of the drive axle system, including assembly, disassembly, troubleshooting, and preventive maintenance. Each section is designed to give technicians a clear understanding of the proper techniques and tools required. As these machines are often used in demanding environments, knowing how to properly maintain and repair them can extend their operational life and minimize downtime. For anyone needing a reliable reference, this manual provides the instructions necessary for meticulous repair work.
Assembly and disassembly procedures are covered in great detail, with step-by-step instructions that are easy to follow. The Clark Shop Manual ensures that each component of the drive axle is properly handled and reassembled to factory specifications. This includes the proper torquing of bolts, correct alignment of gears, and ensuring that all seals and bearings are appropriately handled. Consequently, by adhering to these guidelines, technicians can avoid common mistakes that might lead to equipment failure.
Troubleshooting common issues is another critical aspect covered in this shop manual. Through detailed diagrams and descriptions, users can identify potential problems and their solutions. Whether it's unusual noise, vibration, or leakage, the manual provides diagnostic tips and corrective measures. This troubleshooting section is invaluable because it allows for quick identification of problems, thus reducing the amount of time equipment is out of commission.
Preventive maintenance is perhaps one of the most critical sections of the Clark Shop Manual. Regular maintenance procedures are vital for ensuring the longevity of the FD-17000, FD-19000, and FD-24000 drive axles. The manual outlines routine checks and maintenance tasks that should be performed at specified intervals. These tasks include inspecting and replacing parts before they fail, lubricating moving components, and checking for wear and tear. Implementing these procedures can prevent minor issues from becoming major repairs.
In conclusion, the Clark Shop Manual for the FD-17000, FD-19000, and FD-24000 Series Drive Axle is a comprehensive resource for technicians. Its clear and detailed instructions help ensure that maintenance and repairs are performed correctly and efficiently. By following the procedures outlined in this manual, users can greatly enhance the reliability and longevity of their drive axles while minimizing operational downtime. Having this manual on hand is a crucial part of any maintenance toolkit for those working with these specific drive axle models.